What is Calibration? Definition, Types, Process, and Benefits
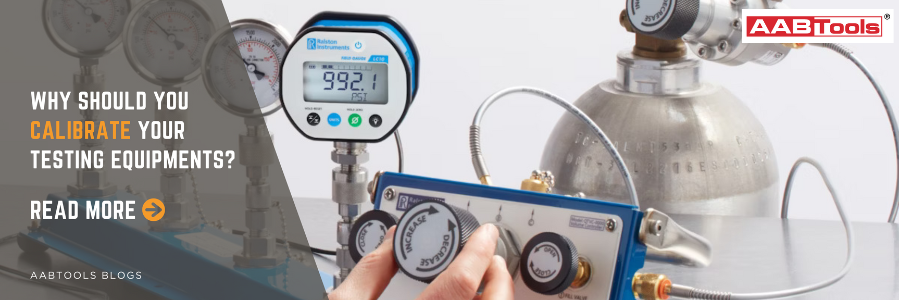
Did you know that even the tiniest measurement error could lead to costly mistakes, safety hazards, or complete product failures? In precision-driven industries, there’s no room for error, this is where calibration comes in.
It ensures your testing and measurement equipment is always accurate and reliable. Whether it’s electrical, pressure, or temperature instruments, regular calibration keeps everything running smoothly and safely.
Numerous studies and reports highlight the serious risks and consequences of using uncalibrated equipment.
Inaccurate measurements from uncalibrated equipment can result in product defects, inconsistencies, and higher rejection rates, affecting productivity and quality.
Miscalibrated devices such as pressure gauges or temperature sensors can create unsafe conditions, increasing the risk of accidents or even fatalities.
Uncalibrated equipment drives up operational costs through inefficiencies, wasted resources, and potential product recalls.
These findings underscore the critical importance of calibration in reducing errors, ensuring safety, maintaining quality, and achieving compliance across industries.
Some of the famous brands in calibration are Fluke and Extech, which are well-known for their precision and reliability in testing and measurement.
In this guide, we’ll explain what calibration is, why it’s important, the different types of calibration, how the process works, and how AABTools can help you maintain top performance with expert calibration services in the UAE.
What is Calibration?
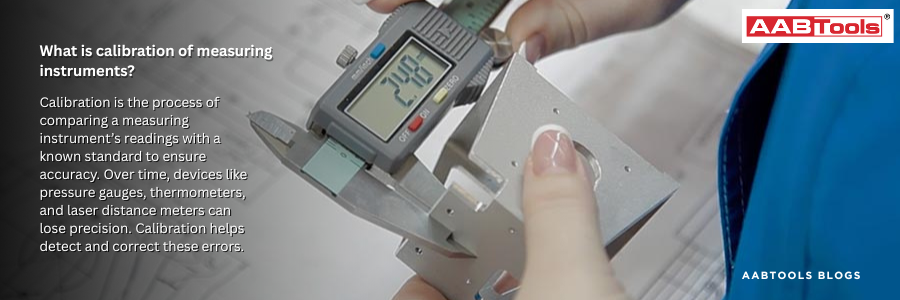
Calibration is the process of verifying and aligning a measuring instrument’s readings with a trusted standard to ensure accuracy. Think of it as a quality check to confirm your tools are delivering precise results. Over time, even the most reliable equipment can lose accuracy, leading to slight measurement errors. Calibration of instruments ensures that your tools are properly adjusted and operating at peak performance.
What is the Purpose of Instruments Calibration ?
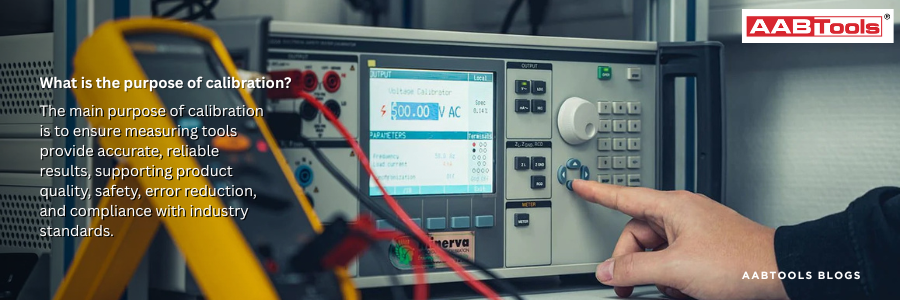
The main goal of calibration is to make sure your measuring tools give precise and reliable results. This is important for:
• Ensuring product quality
• Reducing costly errors
• Keeping workers and systems safe
• Meeting industry regulations
For example, in electrical testing, an uncalibrated multimeter might show the wrong voltage, leading to a faulty repair or even safety risks.
Ensuring equipment accuracy and reliability requires practical and effective calibration practices.
Effective Ways to Optimize Your Calibration Process
Establish a Regular Calibration Schedule
Determine how often each piece of equipment requires calibration based on manufacturer guidelines, usage intensity, and environmental factors. Group devices according to their calibration intervals, e.g., monthly, quarterly, annually.
Utilize software tools or calendar systems to schedule reminders for upcoming calibration tasks. Develop a clear SOP outlining calibration steps, necessary tools, and assigned personnel.
Implement Calibration Stickers
Attach stickers to devices to display the last calibration date and the next due date. Adopt a color-coded system to indicate calibration status e.g., green for up-to-date, red for overdue.
Include the name or ID of the technician who performed the calibration for transparency and accountability.
Maintain Comprehensive Calibration Logs
Use either digital tools or physical logbooks to document all calibration activities. Record equipment ID, calibration dates, results, adjustments made, and the next scheduled calibration.
Retain historical records to identify trends, recurring issues, and ensure compliance during audits.
Train Your Team
Equip staff with proper training on the importance of calibration and how to adhere to established schedules and procedures effectively.
By implementing these practices, businesses can minimize errors caused by uncalibrated equipment, ensure compliance with industry standards, and optimize overall operational efficiency.
The Role of Calibration Across Key Industries
Calibration is a critical process in ensuring accuracy, safety, and operational efficiency across various industries. In all industries, calibration is indispensable for maintaining high standards of quality, safety, compliance, and efficiency.
By prioritizing these practices, businesses can ensure their operations remain accurate, reliable, and cost-effective.
Different Types of Instrument Calibrations
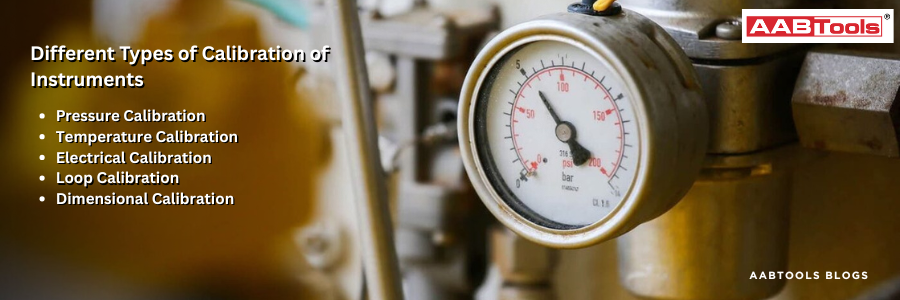
Calibration is classified based on the specific physical quantity being measured. Here are the main types:
Pressure Gauge Calibration
Pressure calibrators are designed for devices like pressure gauges and transmitters, This type ensures precise and reliable pressure readings critical for various applications.
Temperature Calibration
Temperature calibrators are essential for thermometer calibration, RTDs, and thermocouples. This process guarantees accurate temperature measurements, enabling effective temperature control in systems.
Electrical Calibration
Electrical calibrators are used with devices such as multimeters, ammeters, and voltmeters, Electrical calibration ensures dependable and accurate readings of electrical parameters.
Loop Calibration
Loop calibrators are focused on 4–20 mA current loops in control systems, Loop calibration is vital for maintaining precision in process industries. The most common Instrument is the Fluke 789 meter, highly preferred by electricians and other professionals.
Dimensional Calibration
Dimensional Calibrators are used for tools like micrometers and calipers, this type ensures accurate measurements of length, thickness, or other dimensions essential for quality control.
Calibration Process: Step-by-Step Overview
Visual Inspection: Begin by checking the tool for any visible damage or signs of wear.
Reference Alignment: Compare the tool against a certified reference standard to assess accuracy.
Adjustments: If the tool is found to be out of specification, make the required adjustments or repairs.
Accuracy Testing: Conduct multiple tests to verify consistent and reliable performance.
Certification: Issue a detailed calibration certificate documenting the results and ensuring compliance.
The Benefits of Calibration for Testing Equipment
Ensure Accuracy and Reliability
Even trusted tools from brands like Fluke and Extech can lose accuracy over time. Regular calibration ensures your equipment provides precise readings when it matters most.
Prolong Equipment Lifespan
Properly calibrated tools operate more efficiently, reducing unnecessary strain and wear. This not only enhances performance but also extends the life of your equipment.
Meet Compliance Standards
Many industries require calibrated tools to adhere to ISO, IEC, or safety regulations. Staying compliant not only prevents legal complications but also builds trust with your customers.
Best Extech Calibration Tools In UAE
Why Choose Calibration Services from AABCAL in UAE?

AABTools proudly offers professional calibration services through AABCAL. its state-of-the-art in-house calibration facility. Here’s why AABCAL is the trusted choice for reliable calibration:
- Expertise in calibrating premium brands like Fluke and Extech
- Quick turnaround times with precise, certified results
- Full compliance with international calibration standards
- Services are available for both new purchases and existing tools
At AABCAL, we are committed to excellence by maintaining a robust quality management system aligned with ISO 9001:2015 and ISO/IEC 17025:2017 standards, accredited by the Dubai Municipality - Emirates Accreditation Center. This means our calibration results are globally recognized and traceable, giving you complete peace of mind.
Whether you're based in Dubai, Abu Dhabi, or Sharjah, AABCAL ensures your equipment is calibrated to deliver peak performance every time. Contact us today to learn more about our calibration services
FAQs
What is calibration and its importance?
Calibration is the process of checking and correcting measuring equipment by comparing it to a standard. It is important because it ensures your tools provide accurate, reliable results, essential for safety, quality, and compliance.
What are three uses of calibration?
1. To ensure measurement accuracy in tools and instruments.
2. To comply with industry regulations and standards.
3. To prevent costly errors in testing, production, or maintenance work.
Where is calibration used?
Calibration is used in industrial sectors, including manufacturing, electrical, HVAC, oil & gas, healthcare, aviation, and construction.
What is the principle of calibration?
To compare the measurement of your device against a traceable reference standard and adjust it. This ensures your tool matches the expected values as closely as possible.
What are the three types of calibration?
The main types include:
1. Electrical Calibration – for tools like multimeters
2. Pressure Calibration – for pressure gauges and sensors
3. Temperature Calibration – for thermometers and temperature controllers